The Perfect Storm Affecting Project Timelines and Budgets
It's no secret that COVID-19 has had tremendous and lasting effects on more than just the health and wellbeing of the world. For the architecture and engineering industry, these effects have been felt far and wide. Turnkey projects with quick, efficient timelines are now taking longer and longer to complete, thanks to the absence of materials and technology that cannot be omitted. While typically a great many concessions can be made, architects and engineers worldwide, including right here at HFA, have had to seek out alternative solutions or build in buffers within project timelines to account for these shortages.
We recently sat down with HFA Team Lead/Architect, Steven Baker (AIA, NCARB), to discuss how he and his team provide their clients with alternatives that are more readily available (albeit sometimes more costly) to keep their projects on schedule.
High Priority, Low Stock
“At the beginning of each project, we’ve had to empower our contractors to do what’s best to get us to the finish line of a project which involves a lot of communication. At the end of the day, compromises must be made,” said Baker. “When we discuss these shortages with our clients, we ask, ‘Do we want to compromise on what we wanted in a particular material, or do we want to compromise on when we thought we were going to open the store?’ Almost every time, the answer is getting the store opened as quickly as the shortages and supply chain issues allow.”
So, what were the hardest hit industries? Let’s look at a few that have had the most impacted timelines and cost implications:
Lumber
One of the most talked-about and earliest affected material shortages post-COVID was lumber. The material shortage heard around the world, if you will. Whether you were affected by this professionally or personally, lumber prices continue to be cost-prohibitive and require a larger budget, level-set expectations, or both.
For the most part, many in the industry are having to come to terms with these prices as the "new normal" because without lumber, many clients would be unable to complete projects at all. Therefore, it is more crucial than before to have open lines of communication between clients, contractors, and architects to ensure that the building process is as smooth as possible, preventing lumber prices and delays from being the sole reason a project stalls out or completely ceases to exist.
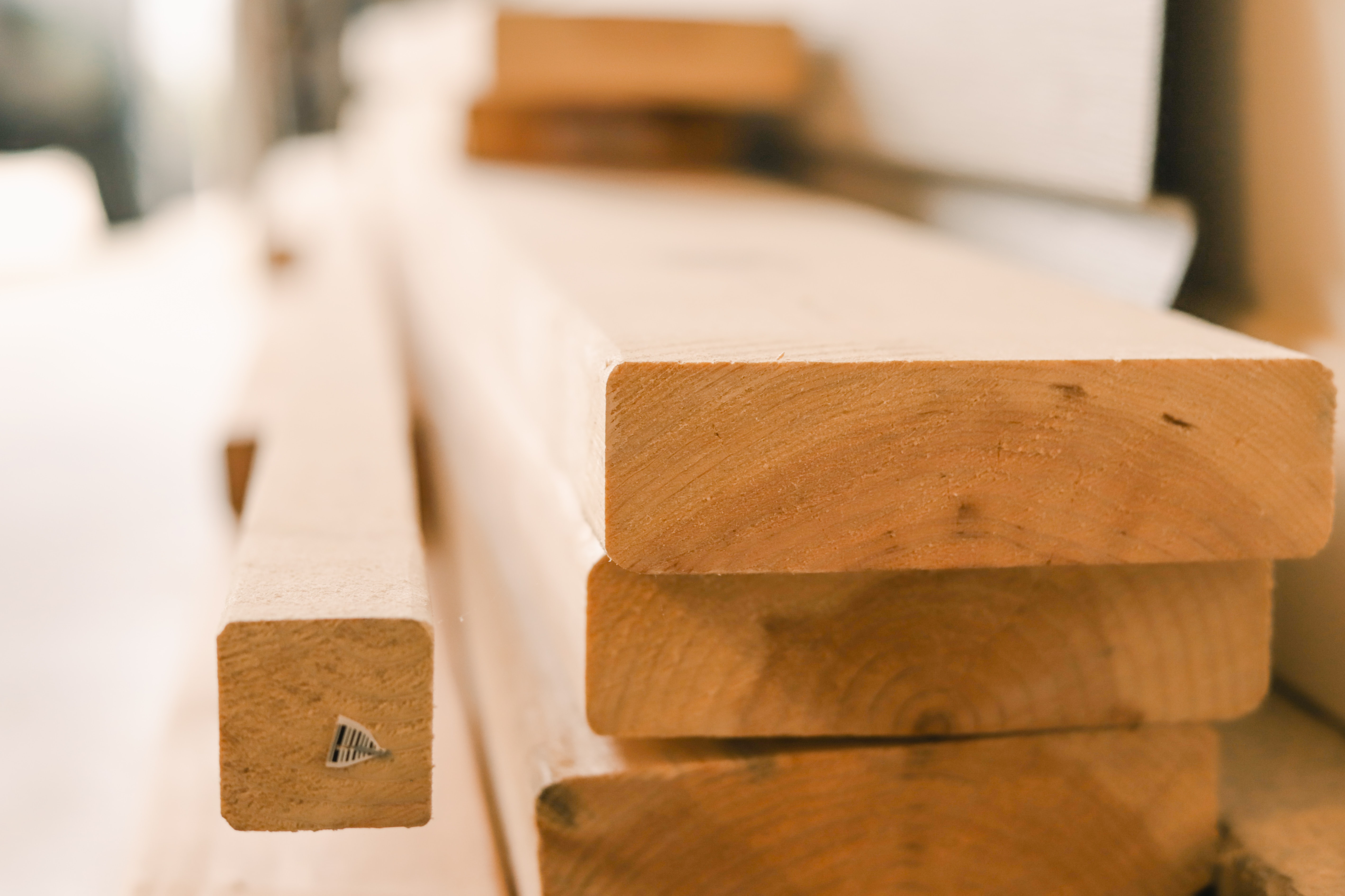
In fact, according to one survey, lumber prices reached their peak in late May 2021, hitting an astounding $1,514 per thousand board feet, in comparison to $349 per thousand board feet in April 2020 (Source: NPR).
While many of today's projects are primarily stick-built, others have been able to pivot, instead opting for metal trusses or other complementary materials that keep the project on track for completion. However, the market for metal materials isn’t without its own complications today, either.
Structural Steel, Steel Joists, & Metal Deck
One of the most economical building materials for framed building structures is steel in the form of structural steel beams and columns, steel bar joists, and metal decking. Due to high demand, the lack of steel joists and metal decking is causing headaches for contractors around the country. Owners are having to delay their opening dates or pay premiums for alternate framing designs. One of the many reasons the industry loves the use of steel building materials is because of its inherent strength, capability for spanning large spaces, ease of erection and construction.
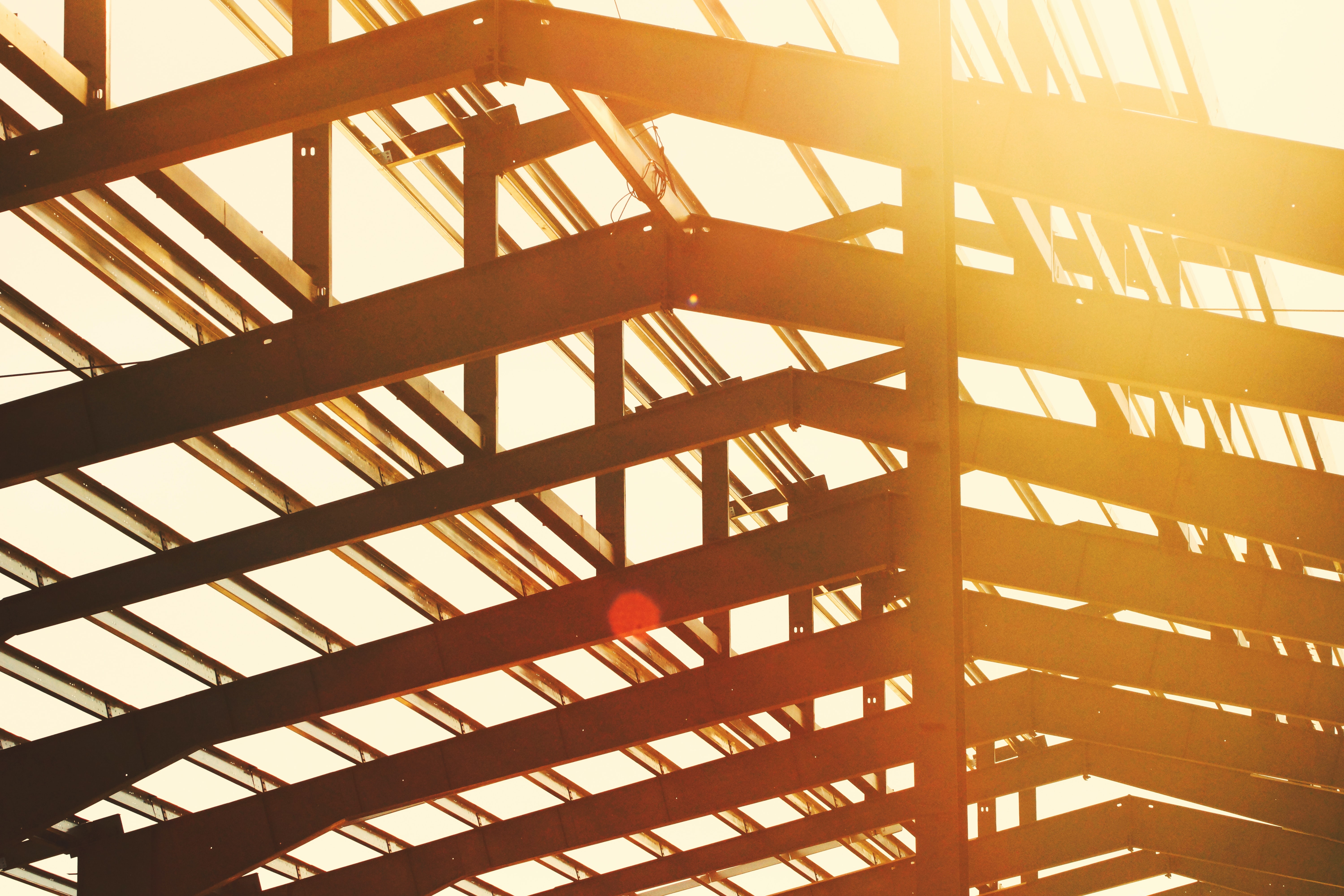
With the run on these steel building materials, building owners challenged HFA to think out of the box and come up with alternate framing systems which were still affordable and enabled them to meet their building turnover dates. These requests usually came at the 11th hour after the contractor recognized the framing shortages.
We investigated alternatives, such as using whole building steel beam framing systems, wood truss systems, light gauge steel truss systems, castellated steel beam systems, or a hybrid of two systems. The use of plywood decks for roofs or cast in place concrete slabs for floors in lieu of using the scarce metal deck systems was investigated for several projects. Each system alternate had its advantages and disadvantages. We worked with the project contractors in developing the right alternate for each project.
As expected, the ripple effect of switching to wood, light gauge, plywood and the like have caused those materials to be in a higher demand, thus creating more shortages.
Fixtures
As projects got closer and closer to completion, our teams began to see the same manufacturing and fulfillment delays with finishing fixtures, as well. During the height of these supply chain delays, lighting fixtures could be delayed up to 24 weeks in some cases (Source: Interior Architects).
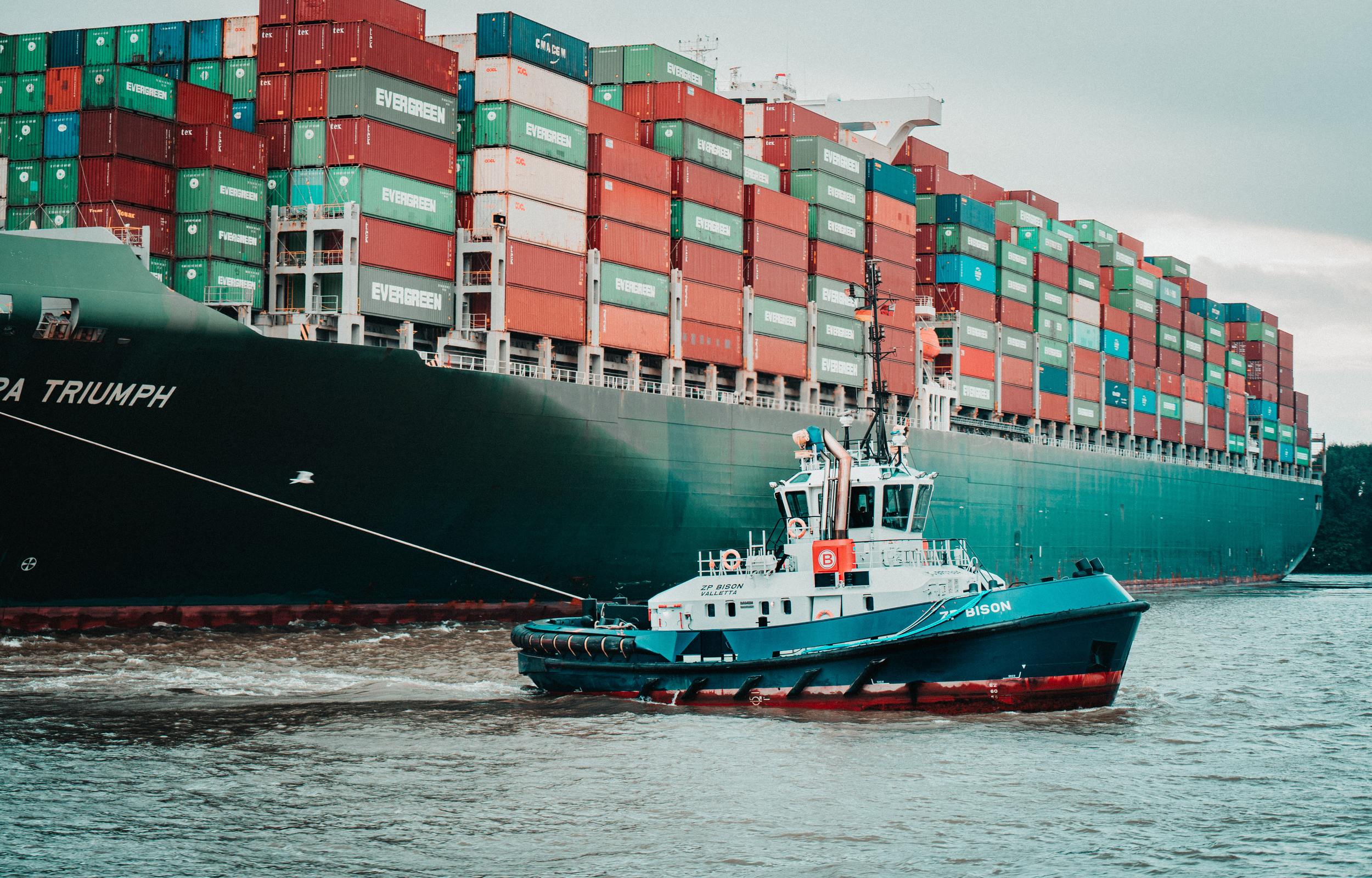
From the lighting fixtures (specifically LEDs) to exterior light poles and everything in between, our teams and others throughout the U.S. industry had to make allowances for specific products being out of stock. In many cases, our team could easily switch out comparable products that may not have been the exact specification that the client desired. Still, it was similar enough to make them happy and keep the project on track.
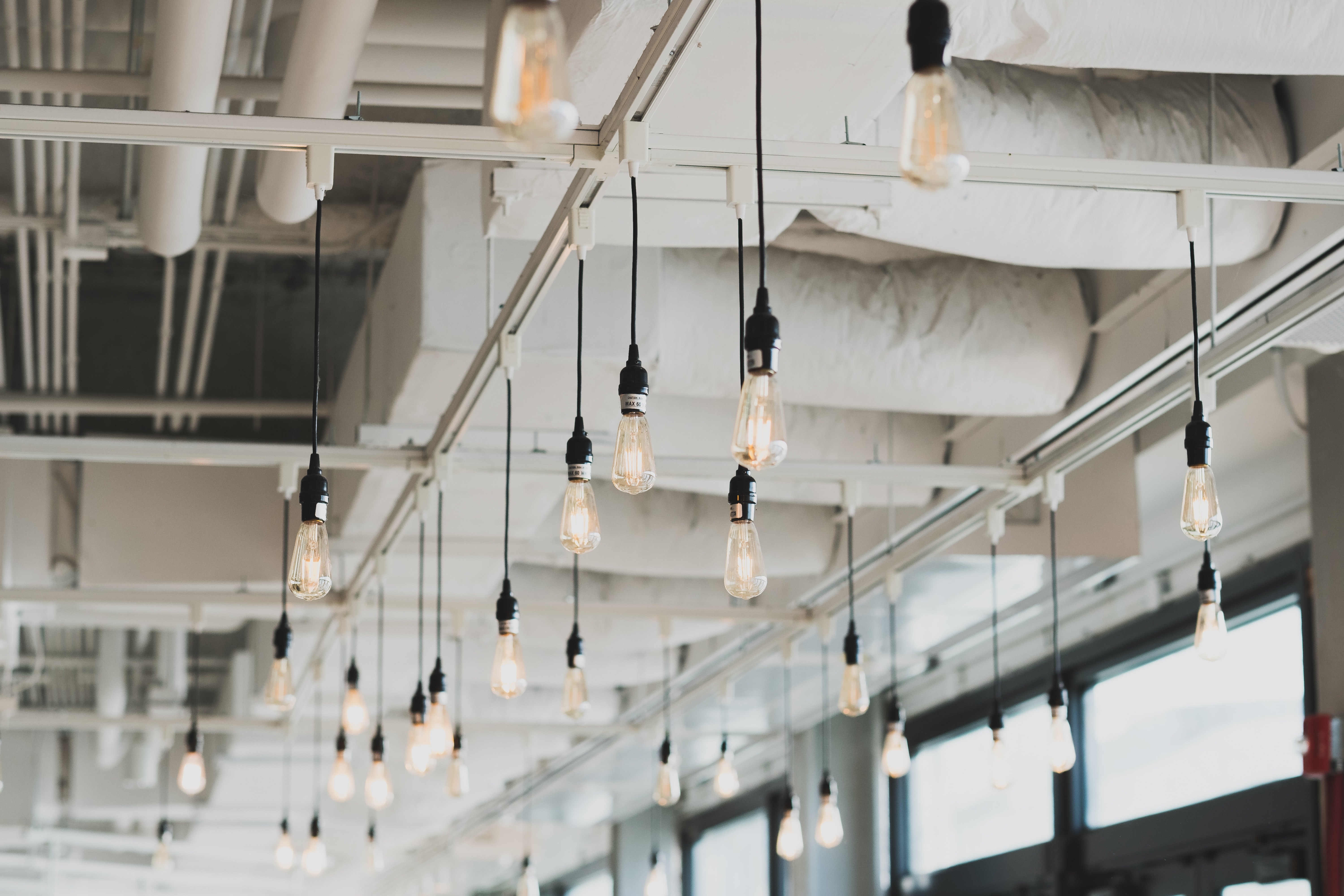
For the most part, our clients have accepted these shortages with grace, and we have been able to work through them without much difficulty. However, there will come a time when our teams need to revisit a few of these projects once certain fixtures are available (e.g., dimmable light switches, etc.) and make the updates for our clients.
HVAC Systems
One of the least flexible material shortages we're currently seeing coincides with HVAC systems, which adhere to stringent codes and requirements. So, where we are afforded a bit of wiggle room when it comes to finishes or wood vs. metal, HVAC systems supply chain issues have the potential to derail entire projects.
In these cases, we can’t simply swap out systems because of issues with proper tonnage and other fundamental system requirements, which often leads to adjustments in lead times and project completion dates. However, in those projects that have been affected, our team has had to find creative ways to keep the project on track. For instance, installing the HVAC units without the heating component to complete the project and then planning a follow-up trip to install once that component is in stock again. Fortunately for our teams, we’ve found ways to work through these shortages, mitigating significant effects on our projects to date.
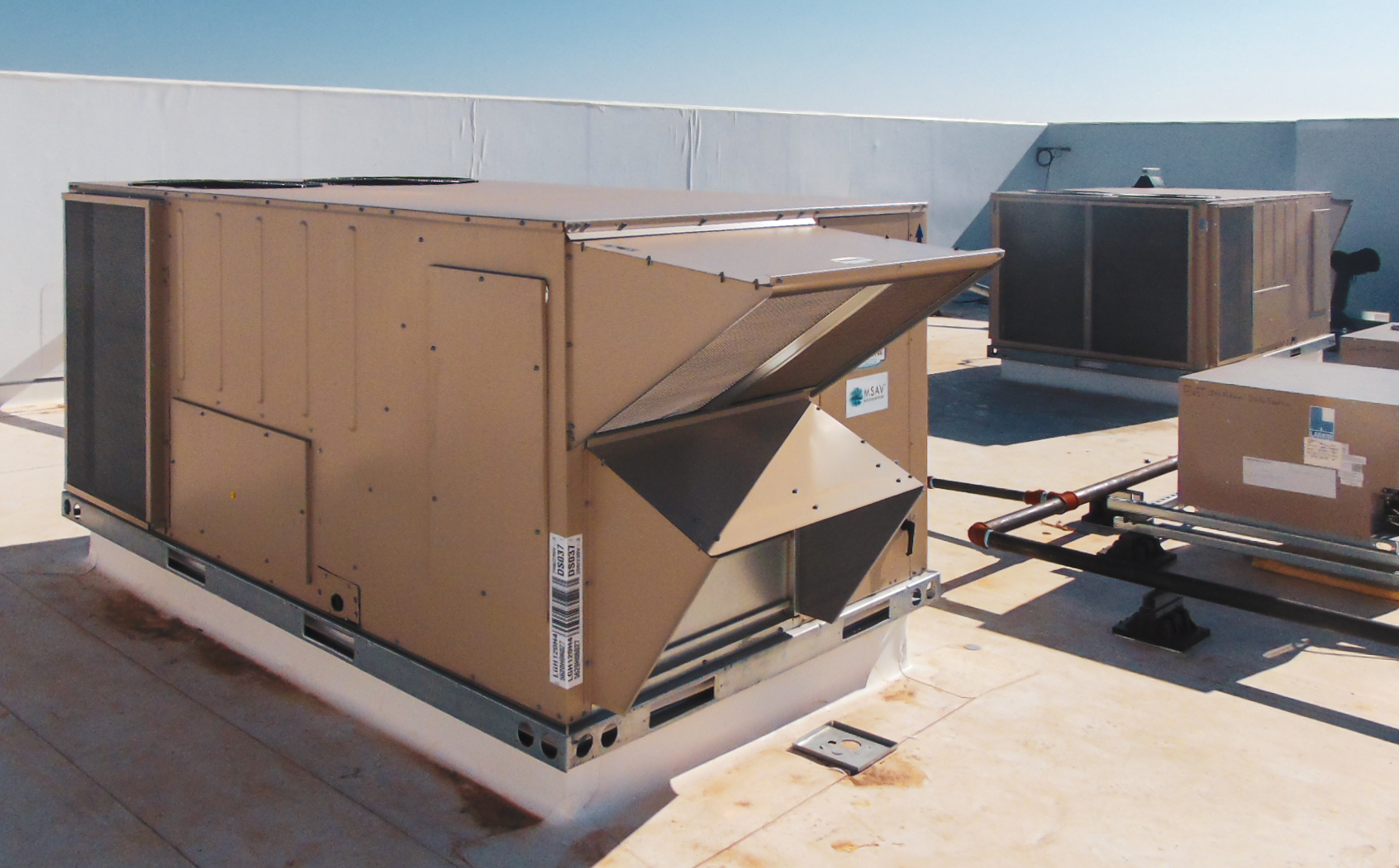
Industry wide, however, HVAC distributors have begun to think ahead and stock as many units as possible, in order to keep up with demand. On average in 2021, HVAC distributors were maintaining inventory levels between 15-25% higher than normal to keep up with increased demand and the resulting supply chain issues (Source: ACHR News).
A New Normal?
We've reached an unprecedented time when faced with higher costs or completely halting a project; clients find those higher costs are often preferable, even welcomed in many instances.
Baker added, "Now we're seeing that it may not even be a specific material shortage in most cases anymore causing the delays, but instead it's a manufacturing problem. Some of these industries are still struggling to keep up with this increased demand for materials, and many are still operating at limited capacity because of COVID restrictions, workers that are out sick, or just a reduced labor force. It can be challenging to keep up."
As restrictions begin to ease, ports reopen, and manufacturers get back to their pre-COVID productivity (or as close to it as they can), those in the A+E industry hope to see some semblance of normalcy. Still, only time will tell if prices and wait times will begin to regulate or if the demand and willingness to pay higher premiums for materials is poised to last long into the future.
Until then, we will continue to partner with our clients and trusted contractors and suppliers to ensure that we provide the same level of service they've come to know and trust, even during trying times when so many things continue to be uncertain. In the months ahead, we hope the supply chain issues begin to level out, and we can see prices and lead times start to normalize once again.